In the complex and demanding world of aluminum processing, the efficiency and longevity of reduction cells are paramount. These cells are at the heart of the aluminum smelting process. Their productivity and lifespan are significantly influenced by the effectiveness of cathode bar sealing.
Mid-Mountain Materials, Inc. has significantly contributed to aluminum processing by developing highly efficient sealing solutions through their THERMOSEAL® M44 Moldable. This breakthrough has addressed the critical challenge of sealing. It has also produced a range of benefits to enhance the aluminum processing industry.
The Basics Of Aluminum Processing
The Bayer process and the Hall-Héroult process can be combined to create Aluminum.
Finding Aluminum
- Aluminum is found in bauxite. This raw material is mined through drilling. Its large layers are made smaller so that they can be easily collected, moved in a vehicle, and then ground down.
- Caustic soda is used to break up the bauxite and aluminum oxide, also known as alumina.
From there, pure alumina can be created through the Bayer Process:
The Bayer Process
Karl Josef Bayer came up with the Bayer process in 1888.
Once the mining process has been completed, the bauxite can be dissolved through a sodium hydroxide solution. After this, red mud, which is created from the impurities of bauxite, can be taken away. This is before the mixed sodium aluminate solution is placed into a precipitator.
After the materials have had their temperature lowered, particles from aluminum hydroxide are added to encourage the appearance of crystals. These crystals are solid and can be removed before being cleaned.
By undertaking this process, you should be left with pure alumina.
The Hall-Héroult Process
In 1886, Charles Martin Hall and Paul Héroult devised this smelting process to create aluminum. It can be used with the Bayer process to change alumina into aluminum.
Once you have your alumina, it is broken down by using molten cryolite. Then carbon anodes use electricity to heat the mixture and keep it at its melting point.
By maintaining the heat, the alumina can be changed into both oxygen and molten aluminum. The oxygen merges with the carbon in the anodes and forms carbon dioxide. This leaves the liquid aluminum on its own and easy to extract.
Aluminum can be delivered in many different shapes and sizes to those who need it. For instance, it can be rolled into thin sheets. Once it has been used, recycling aluminum can make sure that it can be utilized in a different product.
Enhanced Reduction Cell Life
One of the most significant advantages of using THERMOSEAL® M44 Moldable in aluminum processing is the extension of reduction cell life. Proper sealing of cathode bar penetrations is crucial for preventing premature cell failure and maintaining productivity. Mid-Mountain’s solutions ensure that cells are adequately sealed during rebuild operations. Their innovative design and implementation can extend their operational life and ensure sustained productivity.
Exceptional Sealing Efficiency
The THERMOSEAL® M44 Moldable, central to both of Mid-Mountain’s sealing systems, provides exceptional sealing efficiency. Whether through the innovative THERMOPAK® Cathode Bar Seal Boot or the external steel packing gland system, the moldable ensures a hermetic seal that withstands the harsh conditions within reduction cells. This level of sealing efficiency is crucial for maintaining the integrity of the cells. It can also prevent leaks that could lead to efficiency losses or safety hazards.
Versatility and Ease of Installation
A standout feature of Mid-Mountain’s sealing solutions is their ease of installation. The THERMOPAK® cathode bar seal boot, for instance, requires no welding or metal fabrication. This makes it accessible for maintenance teams without specialized skills.
With its easy installation, downtime can be reduced and the maintenance process can be simplified. Therefore it is a cost-effective solution for aluminum smelters.
Tolerance to Heat Expansion
Aluminum processing involves high temperatures, leading to the expansion and movement of cathode bars during start-up.
Mid-Mountain’s sealing solutions, particularly the THERMOPAK® Cathode Bar Seal Boot, are designed to accommodate this initial expansion. They ensure the seal’s integrity is maintained even under fluctuating conditions. This tolerance to heat expansion is critical for maintaining the seal’s effectiveness throughout the life of the reduction cell.
Durability and Resistance
The materials used in Mid-Mountain’s sealing solutions, such as the ARMATEX® SBQF100 and SRF22 fabrics, offer exceptional durability and resistance to harsh conditions within the aluminum smelting environment. These materials are specifically chosen for their corrosion resistance and ability to withstand high-temperature conditions that are prevalent in reduction cells, ensuring the longevity and reliability of the sealing solution.
Customization and Integration
Mid-Mountain’s approach to sealing solutions is characterized by a high degree of customization and vertical integration. The THERMOPAK Cathode Bar Seal Boot, for example, is tailored to fit the specific requirements of each application, ensuring optimal performance. Additionally, the vertical integration of the manufacturing process, adhering to ISO 9001-2015 standards, guarantees the quality and consistency of each component used in the sealing system.
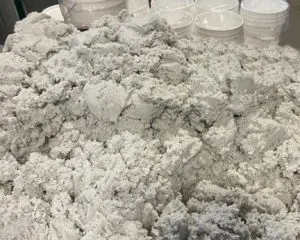
THERMOSEAL® M44 moldable in bulk
Competitive Advantages
The combination of ease of installation, durability, and exceptional sealing efficiency provides a competitive advantage to aluminum smelters utilizing Mid-Mountain’s solutions.
Alongside this, by ensuring the integrity and productivity of reduction with minimal downtime and maintenance requirements, there is an opportunity to capitalize on significant operational efficiencies and cost savings.
Consider Mid-Mountain’s Moldables For Your Aluminum Processing
THERMOSEAL® M44 moldable in Mid-Mountain Materials’ sealing solutions offers a comprehensive array of benefits that address the critical needs of the aluminum processing industry. From extending the life of reduction cells to ensuring their efficient operation and easy maintenance, these innovations represent a significant step forward in the pursuit of efficiency and sustainability in aluminum smelting.