Potlines are an integral part of the large-scale production of aluminium. A potline is a row of serially arranged electrolytic cells (typically 100-400) used to produce aluminium. In a potline, the cathode of one cell electrically connects to the anode of the following cell.
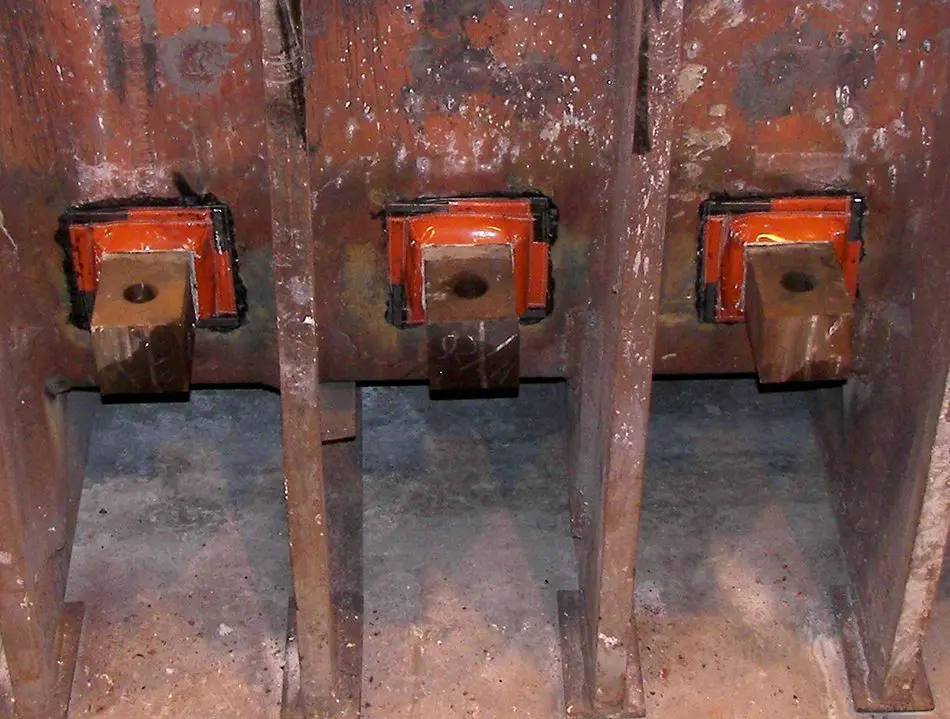
Challenges of Potlines
Thermal losses are one of the biggest challenges industrial potlines face due to poor or neglected thermal insulation.
During unplanned power interruptions, the electrolytic cells lose temperature rapidly, and the electrolyte starts freezing. This rapid cooling of cathodes generates thermal gradients across cathode linings that eventually create thermally induced mechanical stresses, leading to cracking. It impacts both production and maintenance costs, directly affecting production efficiency and incurring heavy financial losses to the organization.
Benefits of Sealing Potlines with High Temperature Seals
Sealing potlines with high temperature seals is a proven solution to maintain heat balance during power failures. Mid-Mountain produces high temperature seals that offer a versatile sealing solution to minimize energy consumption by preventing thermal losses, thus safeguarding potlines against the irreversible and non-repairable damage of cathodes.
The use of high temperature seals optimizes both quality and production, saves relining time, and, most importantly, ensures a sustainable potline operation. High temperature seals also allow effective sealing of furnace doors, which is crucial to maintain positive pressure inside the potline.
While Mid-Mountain manufactures a wide variety of potline seals, two very effective high temperature seals used for potline protection are THERMOPAK® Anode Bar Seals and External Cathode Bar Seals.
THERMOPAK® External Cathode Bar Seals
Mid-Mountain’s patented THERMOPAK® EXTERNAL CATHODE BAR SEALS have solved the universal problem faced by aluminum smelters of how to economically provide a hermetic seal for the full life of the reduction cell, where cathode bars penetrate the sidewall of the reduction cell. In addition to providing an excellent seal for the full-service life of the pot, these boots have the added advantage of providing additional thermal insulation at each of the cathode bar penetrations. Based on Mid-Mountain’s unique silicone-coated fabrics, the boots are die-cut to the exact size required to form a perfect fit, and offer the most improved seal, in the most economical and easy-to-use design ever available to primary aluminum smelters.
THERMOPAK® Anode Bar Seals
In primary aluminum smelters, Anode Bar Seals are used at each anode bar penetration on aluminum reduction cells to reduce the escape of waste gases from the reduction cells into the environment, as well as maintain proper draft control on the fume extraction system for the pots.
Mid-Mountain’s THERMOPAK® Anode Bar Seals are constructed of a specially engineered matrix of fibers, woven into a base fabric, then impregnated with a proprietary compound to enhance temperature, chemical and abrasion resistance in this harsh environment.
The final step in the preparation of the fabric is a top surface sealing compound designed to improve the sealing characteristics of the final product formally known as ARMATEX® SBQKF 451M2.
Where traditional textile seals fail primarily due to the hydrofluoric gas atmosphere, aggravated by the high heat, Mid-Mountain’s THERMOPAK® Anode Bar Seals have been matrix engineered to stand up well to both conditions, in addition to having excellent abrasion resistance.
Portfolio and Benefits of THERMOPAK® Seals
Mid-Mountain Materials, Inc. has been a global manufacturer of sophisticatedly engineered high temperature seals for over 45 years. We offer a diverse portfolio of state-of-the-art cost-effective high temperature seals that address emissions control and thermal protection in a wide variety of industries. Our portfolio includes fabricated components, die-cut gaskets, tadpole gaskets, coated textiles, and high-temperature resistant moldable and cements. and fabricated components, thus delivering the best thermal management practices. Our products can withstand temperatures up to 5000°F (2760°C) while providing chemical and abrasion resistance as well.
References:
- https://mid-mountain.com/solutions/high-temperature-seals/
- H. Kvande and P. A. Drabløs, The Aluminum Smelting Process and Innovative Alternative Technologies, J. Occup. Environ. Med. 56(5 Suppl), S23–S32 (2014). Available at: https://www.ncbi.nlm.nih.gov/pmc/articles/PMC4131935/
- H. A. Øye and M. Sørlie, Power failure, restart and repair, Aluminium International Today Buyers’ Directory (2011). Available at: https://aluminiumtoday.com/content-images/news/Oyeweb.pdf
- A. T. Tabereaux, Loss in Cathode Life Resulting from The Shutdown and Restart of Potlines at Aluminum Smelters, Light Metals, Edited by J. A. Johnson (2010).